After high-profile food scares, European consumers demand higher food standards. Many software suppliers, especially in ERP, do not support users’ requirements for traceability. Some European Collaborative Production Management (CPM) suppliers are tackling this issue by offering integrated Laboratory Information Management Systems (LIMS) and CPM systems. Food & beverage manufacturers are not just implementing traceability as an “insurance policy” against product failure, but are finding that such Enterprise Quality Management (EQM) systems offer rapid payback.
EQM systems can deliver a payback within a year by optimising product values, reducing headcount, and supporting superior plant management. In addition, companies with EQM systems can expect market share gains, improved delivery performance, and possibly enhanced share price performance. Good systems will support sub-lot traceability, splitting and combining lots, and yield analysis.
Bungled product recalls can bankrupt companies. The most spec-tacular example was Japan’s biggest dairy producer, Snow Brand. The company lost US$102.7m between April and July 2000 due to a food poisoning scandal that left 8,000 people sick. Snow Brand, unable to identify contaminated batches, withdrew all its products from retailers’ shelves and shut down 21 plants for 40 days. Workers had routinely recycled milk returned from stores and falsified freshness certificates.
Traditional quality control systems typically use paper logbooks and require production operators to
| |||
A new breed of EQM systems offers more than a “cost of doing business” insurance policy. These systems combine the functionality of a LIMS and a CPM system. Typically, they sit on top of a control system and integrate with the ERP system. Look to the following processes and cost buckets to identify areas where EQM systems improve performance.
Product value optimisation:
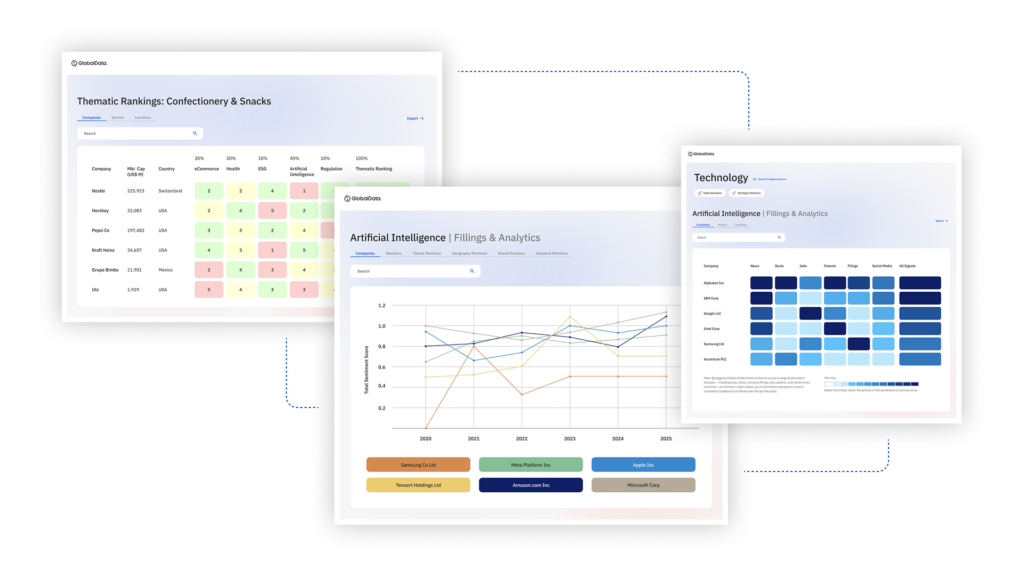
US Tariffs are shifting - will you react or anticipate?
Don’t let policy changes catch you off guard. Stay proactive with real-time data and expert analysis.
By GlobalDataReduced headcount and improved plant management:
Through automating data collection, recording, and analysis, one medium-sized food manufacturer calculated it would save 15 people per production line. Yield losses can exceed 15% in some food manufacturing processes. At times, the cost of failure is higher than the raw material costs, or the lost revenue, since waste disposal costs typically add an additional US$15 per ton. There are also savings in reduced customer complaints and in handling product returns.Paper based quality systems cannot support an analysis of manufacturing performance to identify the source of the problems, such as incorrect equipment settings. Good EQM systems create the performance analysis that enables manufacturers to reduce yield losses by a third.
Improved delivery performance:
Some food industry QA tests require 4 days and occasionally another two days to confirm borderline results. Companies lacking reliable traceability procedures hold finished product in final goods dispatch while waiting for test results. Companies confident of their traceability system can hot-ship. Hot-shipping means transporting product while the lab completes quality checks, so that the final grade is confirmed before the truck reaches the customer’s door. This can reduce delivery lead times by a third, providing for a more rapid turn on cash.Share price performance:
Management’s ability to respond to a food safety crisis can impress equity analysts. During the first few days of a crisis, analysts rapidly decide if the company will recover. For example, Coca-Cola’s share price is still depressed after a 2.5 million bottle recall in Europe. Shares in companies that do recover gain about 5% during the subsequent 50 trading days because analysts positively reassess management’s competence and ability to handle difficult challenges.Traceability challenges
The core of an EQM system is automated electronic record keeping. At a minimum, this means the lot number, specification, operator, time, and authoriser is maintained in a relational database. Better systems include test results and equipment settings and cover all material movements from the inbound weighbridge, holding silos, production equipment, outbound warehousing, as well as with laboratory testing.
| |||
Most systems manage forward and backward traceability. Forward traceability means being able to quickly identify all finished product batches containing a contaminated ingredient, immediately establish their instore or dispatched location and rapidly instigate a product recall. Backward traceability means receiving external notification of a quality breakdown with a product, quickly tracing the affected batch backwards through the process, and easily identifying all associated raw material and ingredient deliveries as well as all similarly effected finished goods batches. There are, however, more complex challenges, so check how your supplier handles the following issues:
Sub-lot traceability:
Often a single production batch might run for a day or longer, and the product characteristics vary during the batch run. Typically, manufacturers might break a 200-pallet batch into sub-lots and sample every fourth pallet. The challenge is to integrate laboratory test results with the control parameters and equipment settings from the control system to see how the product characteristics vary in each sample.Lot splitting and combining:
Often lots are split, and sometimes recombined. In paper manufacturing, a roll is sliced, each slice is processed, and then the two slices are joined together. The best method of checking a software supplier’s capability is to understand the structure of their relational database. Good suppliers link lot numbers, creating a new table for each new lot as a series of parent-child relationships. This provides the flexibility to handle complex multi-step processes.Mass balance:
To fully understand manufacturing yields, managers require a daily mass balance. This function calculates what volume of finished goods should have been produced given the quantity and potency of inbound raw materials. For instance, one litre of water and one litre of alcohol only produces 1.96 litres of finished product.SILO traceability:
Powder silos can lead to poor traceability. If a silo is half full of batch A, and Batch B is loaded on top, then initially batch A drains from the silo, followed by a mixture of batches A and B, and at some point only batch B drains from the Silo. An algorithm that models the draining of the silo is complex, but necessary.Enterprise Quality Management
EQM demands tight integration between a LIMS and the CPM system. Traditionally, different companies develop these two systems, and users must do the integration them-selves and incur additional integration costs whenever they upgrade their LIMS or their CPM systems. But European software suppliers such as Qualtrace based in Ireland, and Compex in Belgium develop industrial strength LIMS and CPM systems. And in the UK, CPM supplier SSI has enhanced its Quality module to replace LIMS systems for many applications. It is only through such integration that rapid payback is possible.
Recommendations:
- Users should tightly integrate their LIMS and CPM systems to fully exploit the ROI potential of these applications.
- CPM suppliers should consider acquiring LIMS suppliers. There are over 200 LIMS suppliers, and many can be acquired at moderate cost.
- Users and suppliers should develop a thorough knowledge of the requirements in US FDA 21 CFR Part 11. Most food, pharmaceutical, and cosmetics companies importing to the USA are required to comply with this Ruling. OEMs in these industries are also affected by the Ruling.