Over the last ten years Logistics has
become an indispensable, competitive weapon within most distribution environments, and
current activity suggests that, if anything, this trend is set to accelerate in the coming
years. The Gartner Group has identified three criteria that represent the fundamental
areas where companies are currently striving for improvement in logistics processes:
Velocity, Variability and Visibility. These criteria apply to all aspects of the Supply
Chain, and optimal logistics performance is achieved through effective management and
continuous improvement in all three factors.
Logistics Velocity
Logistics Velocity is the speed with which
data, planning and execution related activities are performed within the business.
Data velocity
This refers to the speed with which
critical business information such as plans, forecasts, projections etc. are communicated
within the business. A common example of a problem in this area is illustrated by Sales
& Marketing releasing the monthly forecast half way through the month, when
manufacturing needed it at the beginning of the month. The resulting guesswork that
manufacturing is forced to do, leads to inventory shortages, increased carrying costs and
reduced customer service levels.
Planning velocity
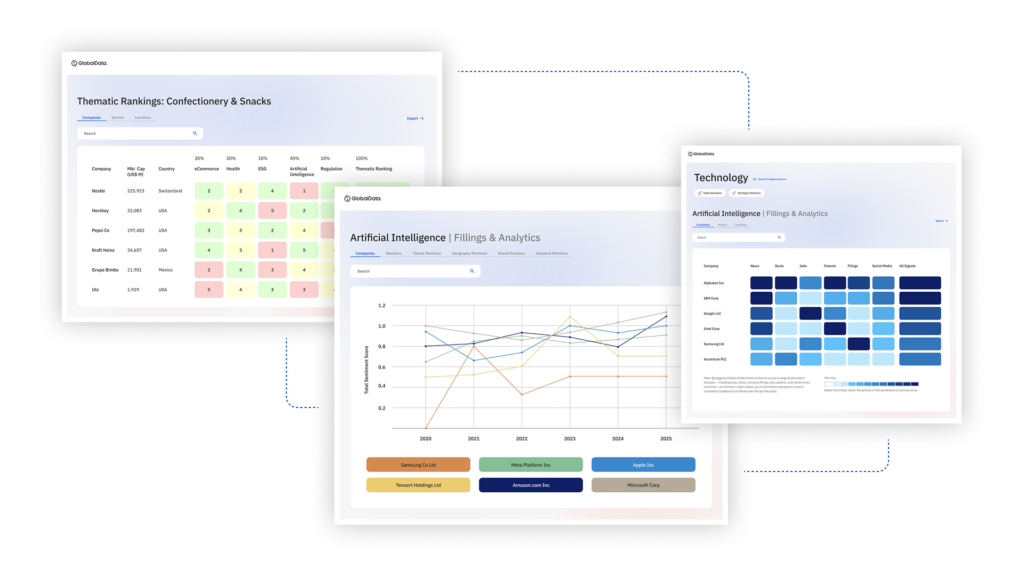
US Tariffs are shifting - will you react or anticipate?
Don’t let policy changes catch you off guard. Stay proactive with real-time data and expert analysis.
By GlobalDataThis refers to the speed with which
schedules can be re-planned, and product mix and transportation can be adjusted to suit.
Improvement in this area may allow a company to move from a monthly planning cycle to a
weekly or event-based cycle, with correspondingly large improvements in the accuracy and
effectiveness of the plan.
Execution velocity
This is the area that most companies have
primarily concentrated on improving over the last few years. Through reductions in
manufacturing, pick, ship and put away lead times, significant improvements in customer
service and inventory levels have been achieved. There is always room for improvement in
this area as any reduction leads to less Work-In-Progress (WIP) and lower carrying costs.
However, achieving the potential for increased responsiveness may be dependent upon
simultaneously achieving greater planning velocity.
Logistics Visibility
Logistics Visibility describes the ability
of a company to extend employee access to internal planning data, extend their own
visibility into external trading partner information and provide trading partners with
access into enterprise data. The overriding objective here is to allow the Supply Chain as
a whole to provide the required level of customer responsiveness, and to move away from
trading partners acting as isolated entities.
This criteria is broken up into the
following sub categories:
Intra-enterprise
As customers place increasing demands on
organizations to provide shorter lead times and greater levels of customization, it is
essential to provide more and more access to enterprise information such as plans and
forecasts to critical employees and departments. Extending visibility here provides a
mechanism by which all parties can assess the impact of their actions across the entire
enterprise. Only in this way will the different departments involved be able to
effectively synchronize their activities to meet the overall profit and sales objectives.
Many users will need to view and manipulate
the same data in slightly different ways, and with considerably different security access,
depending upon their function (operations, finance, marketing, engineering etc). This
produces the need to provide a flexible mechanism by which this can be achieved.
Extended enterprise
Supply Chain performance within any company
can be significantly impacted by its trading partner’s performance. In order to
influence that performance, it may be necessary for organizations to gain access into
suppliers’ inventory levels and capacity constraints. This same concept may also
apply to customers, as visibility of store layouts for example, allows a supplier to
optimize its, and the retailer’s, profitability within each store individually.
Vendors would also benefit through direct visibility into the customer’s production
schedules and forecast information, ultimately using this data to adjust their own
production plans.
Inter-enterprise
Both customers and suppliers are demanding
more and more access to enterprise data, and at any time of the day or night. This
includes a whole range of data, from order status information, to supplier schedules and
customer price quotes. This creates problems from a Management Information Systems (MIS)
perspective, in terms of controlling which trading partners should have access to what
information, and how to deploy so many different perspectives on the same information
efficiently.
Logistics Variability
Logistics Variability refers to the
increasing trend towards customers amending orders right up until, or even during,
shipping and also greater customer specific product and shipping requirements. The former
issue provides customer response benefits through enabling customers to finalize their
order at the last minute, when they have the best chance of providing accurate needs.
However, it plays havoc with supplier’s inventory and shipping plans. The latter is a
growing phenomenon in many industries, with Automotive and Wholesale to Retail (of
Consumer Packaged Goods (CPG) items in particular) leading the way. In both these
industries, compliance to the customers’ procedures, both in terms of shipping
procedures (transportation method, Advanced Shipping Notice (ASN) and documentation
details), and product form & packaging specifications (Floor Ready Merchandise (FRM),
carton labeling etc) is a major service that is considered to be part of the
‘product’ for which the customer pays.
Non conformance to the varying
customers’ procedures (and these very often differ widely, according to their own
‘manuals’ and ‘routing guides’) is often met by ‘fines’ from
the customer. Most commonly this is in the form of Charge Backs, Credits and Deductions
from invoices. This causes a considerable strain on the business systems that must deal
with the complexity of the varying requirements, often unique to different customers.
The problem is exacerbated as these
requirements are continually changing when customers update their procedures, and urgency
is added in an environment where failure to conform adequately leads directly to
significant monetary loss. The traditional method for attacking these issues is through
the implementation of Enterprise Resource Planning (ERP) systems, which provide the
necessary integration and data integrity needed to start identifying the problems and
constraining factors involved. However, these systems by themselves are not enough. Recent
technological advances offer the possibility of even more drastic reductions in data,
planning and execution velocity; significant improvements in the management of order
variability exceptions; and a greater variety of options for Supply Chain visibility, than
were previously available with a typical stand alone ERP implementation.
One example of these advances is
illustrated by ‘Business Process Modeling (BPM)’ tools, which now allow ERP
systems to be implemented according to ‘industry specific’ best practice models.
Typically, implementations do not achieve maximum potential Return On Investment (ROI)
because of the tendency simply to automate procedures that used to be performed manually,
without reviewing those procedures in light of possible efficiency gains.
The BPM step allows the sub optimal
procedures to be identified up front, so that they can be corrected, or at worst
documented with a business justification for continuing to operate in this way. This
implementation methodology can have a particularly significant impact on the logistics
velocity issue, impacting data, planning and execution velocity. Once the modeling step is
completed then the ERP system can be configured according to the task sequence and rules
defined within the model.
In addition, other advances have introduced
the concept of ‘active’, as opposed to ‘passive’, management. This is
especially relevant to the handling of exceptions as they occur within business
operations. Examples where this concept would have an impact are:
- if a large order is booked which consumes a
significant proportion of a monthly forecast, it should be considered as a
‘flyer’, and flagged for potential exclusion from the netting process - an important customer is approaching credit
limit, but hasn’t yet reached it, and it would be advantageous to both parties to
draw their attention to this before it is breached - a critical item has just been scrapped in
the assembly process and the lack of immediate replenishment will have a significant
impact on customer service
In each of these cases, a traditional
passive solution would rely on somebody taking a menu option and calling up an inquiry,
running off an exception report, or pulling up the appropriate view through Business
Intelligence tools before the problem could be highlighted. This may be done at the end of
the day but could equally be delayed until the next exception report at the end of the
week, if such a report exists.
It is now possible to have each of these
exceptions automatically trigger some action in real time, as the event happens. In the
credit limit example, this may result in a friendly, pre-emptive phone call on Monday
instead of an uncomfortable phone call on Friday when the limit has been breached. When
other members of the Supply Chain are involved, as in the critical item example,
notification can be made by the system direct to the supplier, which may potentially lead
to the item being replenished before the customer notices the problem. The resulting
solution offers a mechanism for simultaneously improving Logistics Velocity, Variability
and Visibility problems in one go, with subsequent benefits to customer service, cost
reduction and bottom line.
In the continuing battle for Logistics
performance improvement, incremental change is the norm. The industry in general now has
an opportunity to take a step change as these newer concepts are effectively embraced.