Too many food manufacturers are drowning in an excess of new product development. Solutions are urgently needed. Jonathan Smith and Julie Craig of Axis Management Consulting explain why.
Doesn’t every food company need more new product development? In fact, the answer is “not necessarily”.
For every company we see that is doing too little new product development (NPD), two others are doing too much. Worse than that, much of it is of the wrong kind. A great deal of effort is devoted to projects that are not geniune innovation but just range extension and duplication. In one medium-sized business, we found 99 NPD projects on the books at once, and it is all too common for a company to have more than 50 projects running concurrently. The resulting situation is familiar to many – chaos!
Countless meetings are held as frustrated managers wade through updates on the progress (or otherwise) of a seemingly endless list of projects. The unfortunate project owners bounce between departments trying to get time and resources for their favoured projects. Often the projects that secure the most resources are not the most worthwhile ones.
A cluster of causes
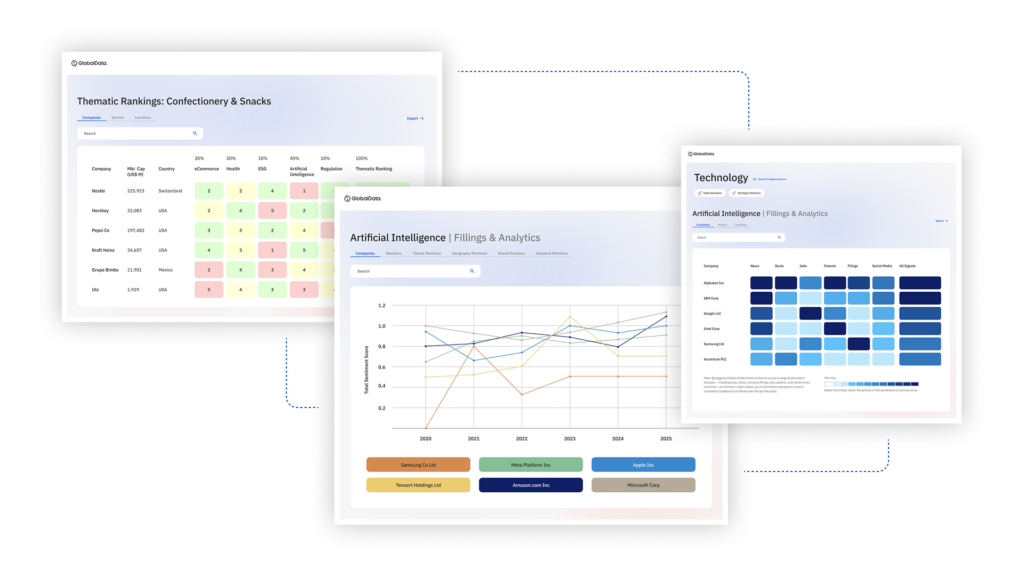
US Tariffs are shifting - will you react or anticipate?
Don’t let policy changes catch you off guard. Stay proactive with real-time data and expert analysis.
By GlobalDataAs with so many business problems, the road to hell is paved with good intentions.
New product ideas spring up from a wide variety of sources, all for the best of motives. Marketeers and salespeople have no monopoly on innovation. Ideas originating with members of the chairman’s family are usually modest in number but unique in their disruptive potential!
Brainstorming sessions, customer requests, and the wish to be seen to be active all compound the problem. With the best of intentions, the temptation is simply to start more and more projects and hope for the best.
Wherever ideas come from, the lack of an effective process for screening ideas leads to too many poor quality projects getting started. Similarly, neglecting to make effective use of consumer research early in the life of a project ensures the continuation of too many ideas that will ultimately fail for lack of consumer appeal.
Another major contributor to excessively long NPD lists is the unwillingness of many managers to kill off projects that are clearly failing. Often people press on, trying to save projects long after there is a reasonable chance of them being successful.
Lack of basic project management disciplines often means that individual projects progress more slowly and clog up the system. Projects are too often managed one step at a time rather than comprehensively from start to finish.
As the number of projects rises, the problem compounds itself. Resources, including management attention, are spread ever thinner. Projects slow down. The number of meetings multiplies, but results are not delivered.
Given all the different forces pushing managers towards NPD overload, it’s an easy trap to fall into. Without systematic efforts to prevent the problem, it will naturally occur.
Commercial consequences
Does all this really matter? Experience shows it certainly does. Too much NPD can significantly dent the bottom line in the immediate term, hamper overall commercial performance and damage customer relationships.
The amount of management time soaked up by a large number of projects represents a considerable hidden cost. The employment cost of the people concerned is just the smaller part of the picture. The real big hitter is the opportunity cost – the contribution they could have been making if their time had been better used.
Ingredients, packaging, and other materials used are the most obvious cost. More projects mean greater disruption to production operations. Plant trials have to be organised. Machine downtime is increased. Staff have to be retrained and redirected. All this causes substantial (and all too often unmeasured) costs.
An excess of variable-quality projects is guaranteed to put further strain on the often fraught relationship between sales & marketing on the one hand, and production and technical teams on the other. Conflict is often increased and mutual confidence decreased.
Ironically, too much development activity can stifle true creativity. If managers are spending large amounts of time on the detail of lots of projects, they will have less time to devote to thinking about the breakthrough innovations that could make a real difference.
Speed-to-market is widely understood to be a critical driver of competitive advantage. If the system is clogged up with sub-standard projects, the good ones get to market much more slowly, or not at all. In the struggle to beat the competition, this is a major issue. If the projects are for retailers’ brands, there is the additional problem of damage to the standing of the supplier in the eyes of the retailers.
Sub-standard projects that actually make it to market before failing incur the greatest costs of all. As well as using up their full share of resources in getting to market, there is the cost of packaging and ingredient write-offs and the management effort needed to manage a withdrawal. On top of this comes the damage to credibility with key customers.
Taking all these effects together, an over-active NPD system is clearly a serious commercial performance issue, and one which happens all too often.
Commonsense cures
So how do you go about minimising these problems?
Make sure that fewer projects of low potential ever get started. This means having a proper screening process, including a small, cross-functional group of managers who are responsible for controlling the overall workload going through the NPD system.
|
Ensure low-potential projects are killed off early. This means frequently re-assessing projects to see if they are on track to deliver the results originally anticipated.
Make effective use of consumer research early on in the process. Too many projects progress to a highly advanced stage without having been seen by a single consumer. Inevitably, this leads to mistakes as managers get too closely involved with projects and convince themselves of the appeal of their own ideas. Consumers, in research, almost invariably give useful feedback that enhances the success chances of projects with potential and prevent resources being wasted on potential failures.
Ensure that projects are moved quickly and efficiently through the system. This means having effective project management – projects being managed to a tight timescale by a team of people who all fully buy in to the importance of the projects.
Less is more
So, in running an effective NPD operation, less definitely is more. A smaller number of carefully selected, effectively managed projects is much better than the chaos we so often see.
The penalties of NPD overload are too serious to ignore. The combination of increased costs in the immediate term, loss of speed-to-market, and damage to credibility with key customers, makes it an important commercial performance issue.
The solutions, whilst taking concerted effort to implement, are within the reach of any company.
By Jonathan Smith and Julie Craig of Axis Management Consulting
Jonathan can be contacted by email at:
jonathan.smith@axisconsulting.co.uk