British Airways World Cargo is re-inventing the perception that airlines only carry perishables goods from ‘A to B’ and is building a dynamic new value-added business in the process.
The airline industry has traditionally earned a chequered reputation with major supermarket chains, perishables importers in the UK and overseas growers. Perishables is a difficult and highly time-sensitive cargo to transport and is only carried by many airlines because there is no alternative on many international routes if they are to generate any freight revenue. Lack of understanding about the special needs of this cargo and poor airport handling facilities often resulted in large insurance claims and a further deterioration of working relationships with airlines.
In 1995, British Airways World Cargo set out to change all that and in four years has developed a multi-million pound ‘business within a business’ that is revolutionising its relationships with perishables customers.
Tony Wright, the airline’s manager of global sales & development, was given the brief to build the airlines perishables business. He says: “British Airways’ unique network meant we had always carried a large volume of fresh produce traffic out of countries in Africa, the US west coast and South America, but like every other carrier, we previously had no special facilities for this business.
” We recognised significant potential if we started to work more closely with perishables customers to gain a clear understanding of their requirements. As a result of this process, in 1995, we opened a dedicated fresh produce centre close to Heathrow.”
Significant Impact
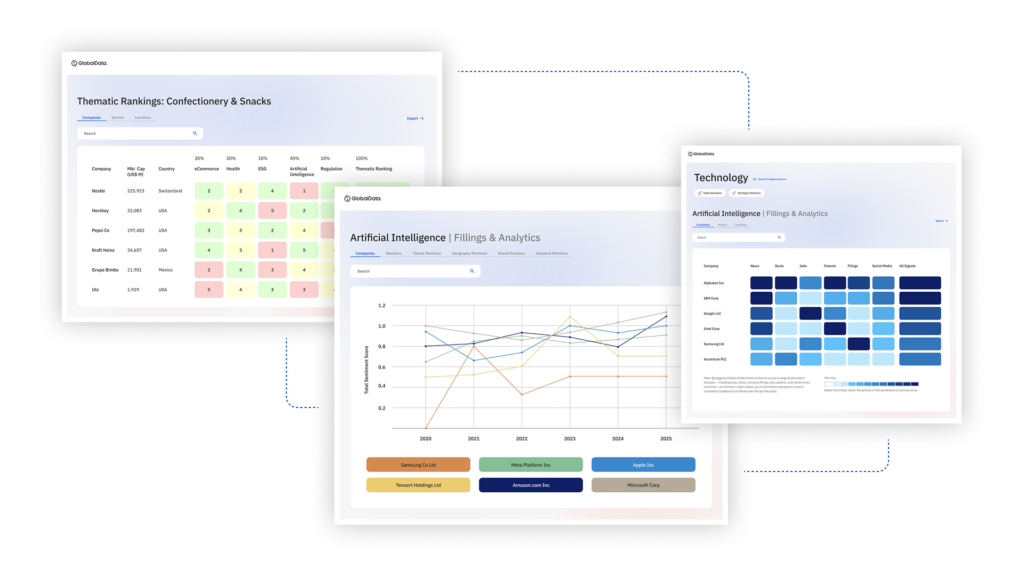
US Tariffs are shifting - will you react or anticipate?
Don’t let policy changes catch you off guard. Stay proactive with real-time data and expert analysis.
By GlobalDataBritish Airways’ commitment and the quality of its fresh produce handling services have had a significant impact. In 1998, it awarded a five-year contract to Christian Salvesen to manage the centre as volume and new opportunities soared. The volume of perishables has climbed from 29,000 tonnes in 1995 to more than 60,000 tonnes last year – but the biggest change is in the provision of value-added services.
Tony Wright continues: “Although it was dedicated to fresh produce business, we quickly outgrew our old facility. We also recognised that it was unsuitable to cope with the new opportunities being offered to us by major UK supermarket retailers.”
£15 Million Commitment
The solution was to find a site on-airport at Heathrow and build a 70,000 square foot Perishables Handling Centre, three times larger than the former building, as part of a £15 million commitment. This opened last August.
The new centre is one of a kind, designed to handle more that 90,000 tonnes a year and with further expansion capacity. Just as importantly, it allows the airline to provide value-added services for a more diverse range of shipments including meat, fish, dairy products and flowers, supported by an on-site Border Inspection Post.
Tony Wright adds: “We have become a significant partner in a dynamic perishables supply chain. Inefficiency in transportation, handling or processing times reduces product shelf life and quality for the consumer. Our importer and supermarket customers simply will not accept that.”
Facilities and Services
Fully temperature controlled, the new centre is helping World Cargo to grow its already strong position in the global food chain. It provides all of the facilities the airline needs to support the efficient distribution of perishables commodities in the UK and Europe. These include container breakdown, quality control, sorting, order preparation, packing, customs clearance and distribution. In addition, the airline now applies one million supermarket labels each month to newly-arrived fresh produce shipments to promote new product lines, price changes and incentives.
The building is designed to handle up to 80 ULD cargo containers at any one time and has 13 delivery and despatch doors to ensure customers’ vehicles are handled quickly. Inside the facility, seven individual cold storage chambers provide dedicated areas for different types of perishable cargo.
On its second floor level, the centre incorporates a packhouse operation where perishables are unpacked, labelled and prepared for despatch in supermarket store trays for specific regional distribution centres.
Commenting on the importance of perishables, Kevin Hatton, managing director of British Airways World Cargo, says: “Perishables is a major part of our cargo business. Today, as consumers, we take for granted that we can walk into any major supermarket in the UK and buy our favourite perishables all year round. We have forgotten that just a few years ago, most of these items were only available seasonally, whilst some of the more exotic fruits and vegetables were once unheard of in this country. This is a tribute to the way retailers, importers and airlines like British Airways are working together.”