The use of integrated computer programs to
help food processing and retailer technical management has developed rapidly over recent
months. International Food Hygiene had a recent opportunity to learn practical issues when
we were invited to join a forum of current and future users.
Senior technical managers from the best of
the UK’s food processing and retail industries had been invited by QSA Ltd.
Wide range of uses
Since the company launched its SmartX
product in early 1997 over 100 production sites have started to use it. These range from
large multi site operators to small independent manufacturers and include multiple
retailers and manufacturers.
Specifications Management and Raw Material
Traceability (SmartX) is a unique Windows based program for managing raw material data and
producing finished product specifications to individual customer formats.
It will, for example, store all raw
material, packaging and finished product specifications, it will configure the set up for
each customer’s requirements and make changes and updates a simple procedure. It can be
integrated with HACCP and LIMS systems.
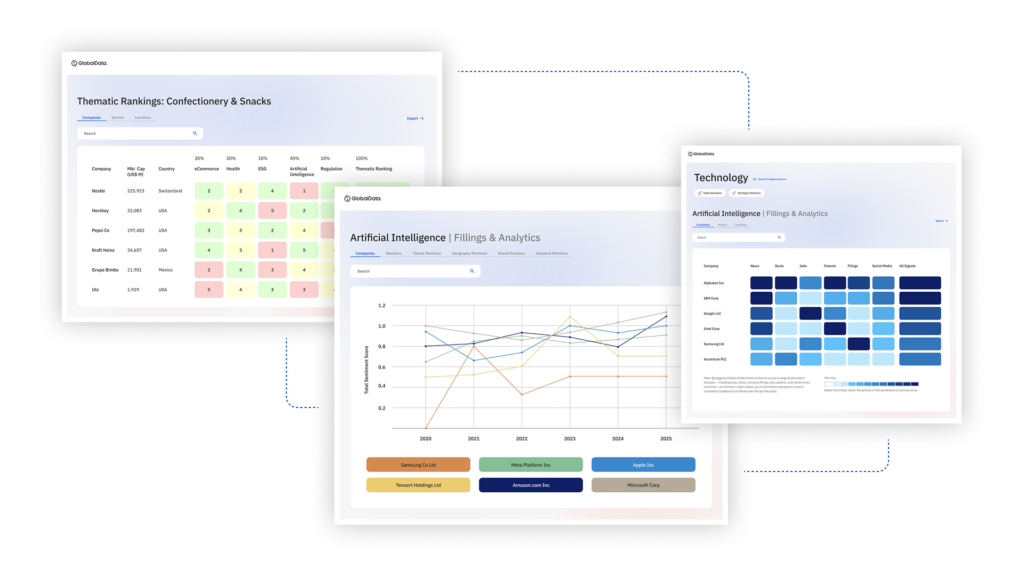
US Tariffs are shifting - will you react or anticipate?
Don’t let policy changes catch you off guard. Stay proactive with real-time data and expert analysis.
By GlobalDataOne of the companies represented was Park
Cakes and their technical manager, David patient, explained that there were two main
reasons for installing SmartX.
Firstly their multiple food retailing
customers were requiring increasing amounts of information and, secondly, with four
production sites the company needed quick and reliable access to data forever increasing
development work and reviews.
The central raw materials database had
proved a great advantage. With a single point of entry and multiple use it had reduced
duplication of effort and improved the flow of information.
As a development tool he expected it would
prove to be very powerful, enabling rapid specification and evaluation of ‘what if’
recipes. The system could then provide the data for label production and ingredient
declarations.
His experience of introducing the system
showed the need for a person dedicated to the task of installation and operation and the
need for customer support in fine tuning the report formats.
That support was shown to be on hand
especially from Bill Wadsworth of Iceland Frozen Foods who was the next speaker.
The company has over 200 own label
suppliers, 2000 specifications and up to 500 product revamps per year. The need for SmartX
was driven by the demand from consumers for more information about product.
“They cannot accept that today’s
retailers do not know what is in their products” he said and the repercussions of BSE
and Genetically Modified Foods have been a powerful illustration of his point.
He also found the increasing needs for
export documentation demanded better informationmore rapidly and the growing needs of
allergic and special interest groups made the management of product specification
information more and more important.
The overall benefits of the system will be
widespread. The central technical team, the QA teams at the company’s eight depots, the
development staff, internal and external laboratories and the sales and marketing teams
had all identified advantages.
The output of paper will be reduced, the
speed of quality assurance checks had increased and the time between product specification
finalisation and ‘right first time’ artwork for labelling will improve.
Significant cost benefits
He showed how a total of three members of
staff had been made available for reinvestment in other duties and the investment in
hardware and software would be paid back in 2 years from all the benefits and savings.
From the first review of the need for ‘some
system’ through to the start up of the SmartX system had been several years, but the
updating of hardware had to be achieved along the way.
In January 1997 all suppliers were informed
of the new system which requires them to confirm specifications and amendments via
diskettes, using Iceland’s format.
The first specifications came in at the end
of January 1998 and as an incentive all new product launches required specifications to be
confirmed on the new system.
The operation is also expected to help,
especially in terms of information quality and speed to launch.
A major benefit during implementation had
been the step by step ‘help’ document for suppliers and the training scheme was so
effective in reducing queries it would become compulsory.
Standard glossary required
The forum the considered two areas of a
similar significance. Peter Kaser of QSA raised the issue of different terms being used by
different groups of the same food products or components and the need for a central
standard glossary was called for. He thought that it would be a great help if a central
government body such as MAFF or ADAS, or even the forthcoming Food Standards Agency, took
responsibility.
In the meantime a start could be made if
SmartX users pooled their current terms for a standard glossary.
Another topic concerning the disparity of
standards was the variations in the different formats for presenting product
specifications to retailers. Each seemed to have their own variation requiring the
duplication of labour in preparing the different formats.
The presence of representatives from
Iceland, Tesco, CRS, CWS and Somerfield offered an opportunity to air this long-standing
problem and the observations from the floor were very encouraging. All the retailers
present were open to the possibility of establishing a standard format.
Bill Wadsworth of Iceland suggested QSA
might propose an ideal standard and Bob Anderson of Tesco said that with forthcoming
changes in their information needs now would be an excellent opportunity to establish a
standard specification format.
As a result interested parties have been
invited to form a working group to look at specification standardisation.
The forum proved to be a powerful way of
pooling experience and expanding the common interests of the software users. It is to be a
regular event and the next is planned for a central venue in October.