An international study shows how the UK
food and drink manufacturing industry benchmarked as ten per cent less efficient as those
in other countries.
Food and drink manufacturing factories in
the UK were compared with those in Japan, the USA and the rest of Europe. The report is
published alongside an action plan for achieving world class manufacturing status for all
UK food and drink companies.
The benchmarking study was conducted by the
UK Food and Drink National Training Organisation (Food & Drink NTO), which is part of
the Food and Drink Federation. The research also reveals that the three most competitive
UK companies all had completed ‘Investors in People’.
The main reason for the poor figures is the
amount of time spent changing over production lines for different product ranges and
downtime due to machine faults and shortages. While high change over time was linked to
the strength of retailer demand (particularly strong in the UK) downtime could be improved
by implementing planned maintenance systems.
Both change over and downtime could be
vastly improved by multi-skilling machine operators. Companies which had the newest, most
high-tech equipment had the highest downtime, largely because their operators had not
received sufficient training at the point of commissioning the plant.
In the companies studied, 30 per cent of
the UK workforce had basic educational qualifications, compared with over 60 per cent in
the EU, and over 70 per cent in Japan.
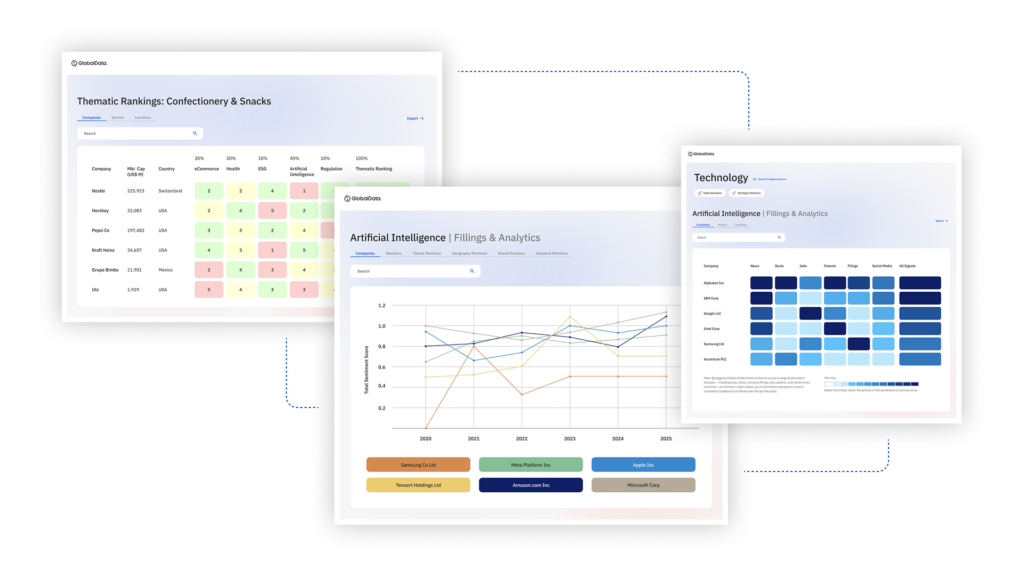
US Tariffs are shifting - will you react or anticipate?
Don’t let policy changes catch you off guard. Stay proactive with real-time data and expert analysis.
By GlobalDataAlthough the UK percentage of employees who
have vocational qualifications is 30 per cent higher than it was three years ago, this is
still way behind the rest of the EU and Japan. To compensate, the UK comparatively spends
the most on training – mainly in the area of health and safety and hygiene – but if UK
companies allocated more of their training budget to developing processing and engineering
skills they would incur less change over and downtime and would be more competitive.
Terry Mills, the chairman of the steering
group and personnel controller at Unigate Dairies said of the findings: “This
benchmarking study shows how sometimes companies are so embroiled in their day to day
running that they risk missing the big picture. Whilst, the study is indicative rather
than conclusive, it does demonstrate that there are many UK companies who could improve
their competitiveness relatively easily and at little extra cost.
“During the study we made some
startling discoveries. We found that companies which had the oldest plant had the least
downtime and were the most competitive. This seemed to fly in the face of conventional
wisdom, until we realised that the companies with the newest equipment had not trained
their operators and maintenance staff at the commissioning stage.”
Details of reports from Food Industry News Click Here