
Tyson Foods, the US meat major and one of the world’s largest, believes the industry will likely quicken its efforts to increase the use of automation in production facilities.
The company, like many of its peers, has seen factories closed amid outbreaks of Covid-19 among staff. Manufacturers across the food industry – and in a number of countries – have seen production staff test positive for the novel coronavirus. Companies have sought to implement more health-and-safety measures to try to protect staff. Some manufacturers have temporarily shut plants for deep cleaning.
One part of the food-manufacturing industry that appears to be a hotspot is the meat-processing sector, in part due to the lack of automation seen in that part of the business compared to other categories.
Tyson has closed a number of processing plants across the US, some having re-opened while others remain shut. The Jimmy Dean and Hillshire Farm owner has, alongside rivals such as JBS and Smithfield Foods, been under scrutiny for how they are operating plants during the pandemic. On Monday (4 May), when Tyson announced its second-quarter financial results, the company’s management faced questions from Wall Street analysts on its manufacturing footprint, including on the use of automation and, more broadly, on production costs while operating during the pandemic, as well as moving forward.
Noel White, Tyson’s CEO, said the company had been investing in automation and said the business and the wider industry would likely hasten those efforts.
“Probably close to a year ago … we started investing fairly heavily in technology, automation, and that hasn’t changed,” White said. “We continue to invest in that segment. I do think that over the course of time that the amount of automation will, in fact, continue to increase, particularly, in some of the more difficult jobs and positions.
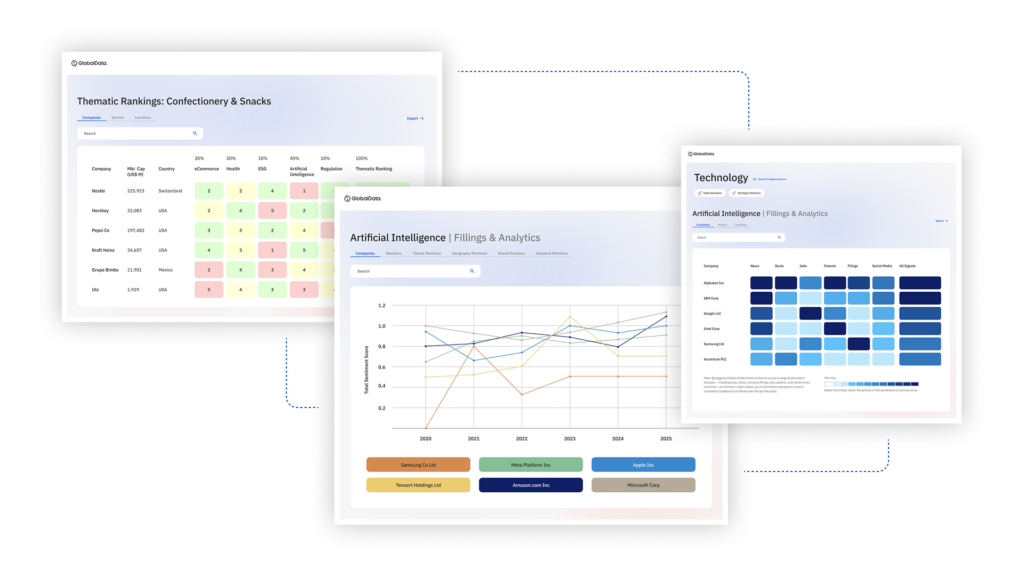
US Tariffs are shifting - will you react or anticipate?
Don’t let policy changes catch you off guard. Stay proactive with real-time data and expert analysis.
By GlobalData“I can tell you that, we as an example, we’ve invested a significant amount of money I would say in our attempt to minimise any foreign objects, where we’re using vision technologies, we’re working in the debone area within poultry, we have a number of initiatives within beef and pork. I believe it’s not only us as a company, I think the industry will continue to look for solves through automation. I think it will likely accelerate from this point.”
Among the measures Tyson has recently introduced into its US processing plants include partitions on production lines and thermal scanners to check the temperature of staff. Dean Banks, Tyson’s president, said those initiatives, combined with running some production lines more slowly, had led to “lower levels of productivity and higher cost of production”, adding: “This will likely continue in the short term until local infection rates begin to decrease.”
On the call with analysts, Tyson’s management was pressed on how much its production costs had risen. Banks said: “We’ve invested substantially in our protective equipment for our team members, including things like chartering planes to supply masks even before they were mandated by the CDC [US Centers for Disease Control and Prevention]. We bought some quite expensive thermal scanners to make sure that we can check temperatures for our team members coming in and out of our plants. Another expense is the inefficiency of the plants driven by the slowing or idling of the plants while they’re being checked and while our team members are being tested.
“Another priority of ours is to keep food on the table of our consumers. And so, that includes running and recovering plants at slower capacities … but also running them with overtime and additional costs to make sure that whenever we can run them in control, we can put food on the American tables. One expense I can quantify is the US$120m in ‘thank you’ bonuses we provided to our team members during this time for the hard work. Again, team member safety being our top priority, it is hard to predict the extent of these costs over time.”
Asked if Tyson was going to see “structurally higher” equipment costs for the business, Banks replied: “As this disease has progressed, as we’ve learned more, anything that we can find or discover that can improve safety in our facilities, we are doing. When it comes to the long-term structural cost of the business, there are some things that we’re installing now. For example, these thermal scanners that we will leave installed and they’ll provide even a benefit whenever we move into the next flu season to just help our team members better understand they’re starting to develop sickness early and that sort of thing. But no, it’s not possible to really quantify or put a number on what those costs are going to look like related to Covid-19.”