An international benchmarking study today showed that the performance of the UK food and drink manufacturing industry has improved over the last three years – but only by 0.5%. This still leaves the UK behind Japan, the USA and the rest of Europe. The report, published by the Food & Drink National Training Organisation (NTO), identified areas for improvement as:
· changeover time spent altering production lines for different products and recipes;
· downtime due to faults and breakdown;
· output rates, although in many cases this was because of unrealistic targets;
· waste and yield, although this has improved considerably in the last three years;
· skills shortages; and
· training and development.
Food & Drink NTO also published an action plan to help companies continue to improve their performances.
Tom Evans, Chief Executive of Food & Drink NTO said:
“Ironically, many of the factors hampering the competitiveness of the industry are related to fulfilling retailer and ultimately consumer demand. In the UK, the customer is king: the study found a high level of order satisfaction – higher than the rest of Europe and the USA. Retailers in the UK have much wider product ranges than anywhere else in the world. This provides more choice for consumers, but results in a higher level of changeover time for manufacturers. Changeover time is directly linked to output and yield and so is a major factor in determining our competitiveness. One of the recommended points of action is that sales teams should develop a good understanding of production processes when scheduling orders and should work with retail buyers to explore mutually beneficial ways of reducing product ranges.
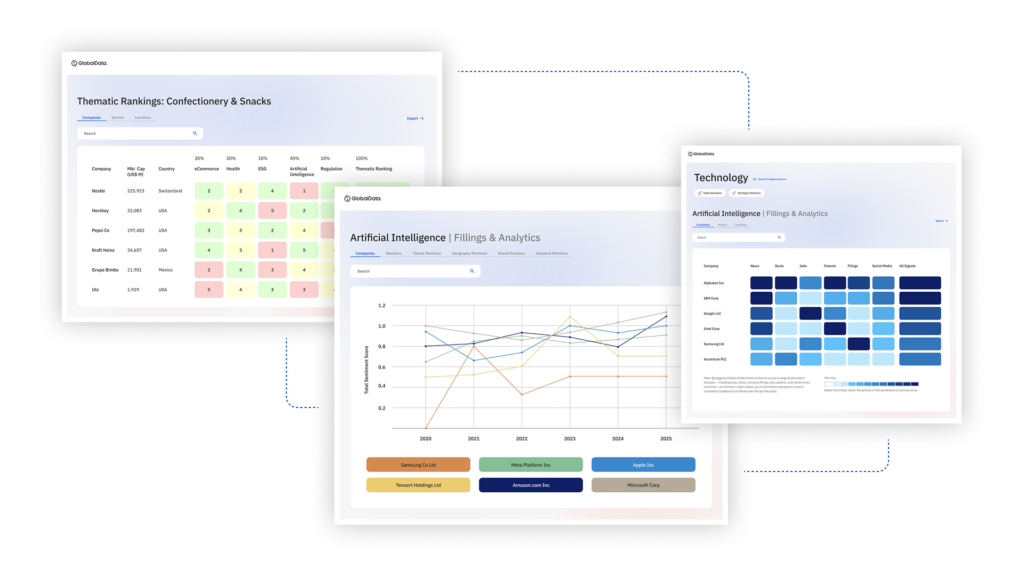
US Tariffs are shifting - will you react or anticipate?
Don’t let policy changes catch you off guard. Stay proactive with real-time data and expert analysis.
By GlobalData“Training and development, on the other hand, is something that the industry can tackle independently and will have a beneficial impact on downtime. Companies need to match their training programmes to job specifications, and very importantly need to build training into the planning, purchasing and commissioning of new equipment at a very early stage. One reason companies with new equipment have high levels of downtime is that employees are not trained sufficiently in how to use new plant.
“There have been some real gains too. Despite problems with changeover, output has increased by around 7% and ‘right first time’ has improved too. There has been heavy investment in plant and Research and Development over the last few years and we would expect to see that pay dividends in future studies.”