According to a study financed by Lawson Software, many food companies are failing to efficiently manage the supply chain – meaning that they are failing to optimise customer service levels and profitability.
The research, conducted by Enterprise Economics on behalf of Lawson, focused on the working practices of 200 leading food companies in Europe, Australia and New Zealand, and Asia. It revealed that many food companies routinely face excess inventory or empty shelves due, the report suggests, to the continued use of spreadsheets or paper-based methods for sales, production and purchasing planning. This, Lawson said, can impact sales and have serious consequences on the bottom-line for retailers and manufacturers alike.
The study found one in four Asian companies use paper for sales forecasting and planning, compared to one in a hundred in Europe. European companies take the lead in utilising planning software for sales forecasting, with 58% doing so compared to 36% in Australia and New Zealand and 13% in Asia.
However, while European businesses are more likely to use advanced planning tools, 21% still use spreadsheets for production planning and 30% use them for sales forecasting.
Lawson suggested that the use of manual planning methods often leads to data errors, particularly in relation to seasonal peaks of supply and demand, increasing the likelihood of producing flawed forecasts.
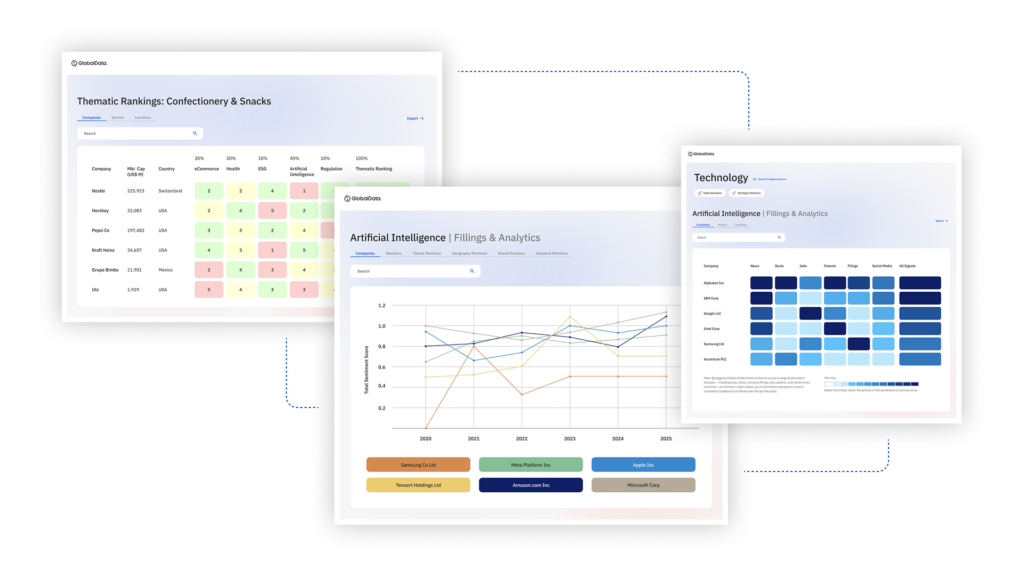
US Tariffs are shifting - will you react or anticipate?
Don’t let policy changes catch you off guard. Stay proactive with real-time data and expert analysis.
By GlobalData“The food and beverage industry has very small margins and is very dynamic,” said Alun Baker, vice president for North West Europe for Lawson Software. “As such, accurate supply chain information is absolutely key, not just for planning, but also for operational efficiency. Many food and beverage businesses still have a great opportunity to take advantage of the modern technologies available that can help them increase their level of customer service, create new operational efficiencies, reduce risk, and increase profitability. It’s still a vastly untapped area of supply chain management.”