
Unilever has launched an “agile food factory” in the Netherlands the company suggests will provide it with flexible production lines.
The FMCG giant’s engineers have designed a manufacturing unit that operates within a 40ft sea container and which, the company said, can be moved all over the world.
Unilever said the unit was developed for liquid boullion but the company hopes to use the technology for other food products, such as ice cream, ketchup and mayonnaise.
The factory is being trialled in Wageningen in the Netherlands, the town that is home to Unilever’s global food R&D site.
Unilever said the unit can be shipped to new locations across the world, making the most of local ingredients and allow quicker responses to changing demand in local markets. Products can be rolled out faster, it suggested.
The model can also be used to produce small volumes for product trials, without the need for mass production lines.
The factory is remotely run by a central “platform eco system” that uses live production data. Sensors on the line feed data back continuously, so adjustments can be made and problems quickly fixed.
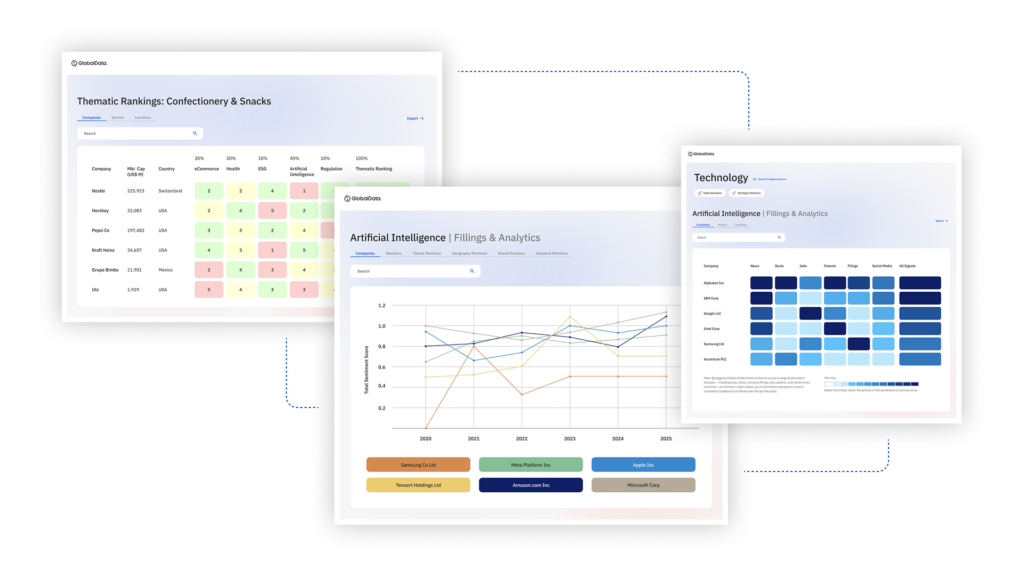
US Tariffs are shifting - will you react or anticipate?
Don’t let policy changes catch you off guard. Stay proactive with real-time data and expert analysis.
By GlobalDataUnilever plans to lease, rent or sell these production units to young entrepreneurs, “opening up the opportunity for new ways of working to others”.
Olivera Trifunovic, Unilever engineering manager and project lead, said: “This travel factory reflects a new dynamic model where thousands of nano factories could be run from a central system, allowing us to have flexible production lines wherever, and whenever, needed.”
She told just-food the unit can be used for both retail and foodservice productions. “The travel factory has the ability to produce both types of products in certain pack formats,” she said.
Trifunovic added: “Unilever has over 300 factories across 69 countries and many of these are big facilities that are designed to manufacture products in large quantities, at high speed. But sometimes we need to produce a small volume (perhaps a seasonal variant) or test a product before launching it. It’s not commercially (or indeed environmentally) viable to use a mass production line for this.
“The intention is never to match the output of a large factory, but if needed we can incrementally increase production with any number of these units. Ultimately, a network of travel factories gives us greater flexibility in our supply chain. A dynamic model like this could see thousands of local production lines all across the world.”