ConAgra Foods has provided an update on its reorganisation announced last March, including five closures and a workforce reduction of approximately 400 employees.
The company is closing its Archbold and Fort Worth locations, and its tomato paste production facility in Helm will operate on a seasonal basis only, and other product volumes will transfer to Oakdale.
ConAgra’s Rossford plant is also closing, with production moving to the company’s Waterloo and Menomonie plants. Production at its Folcroft snack plant, also due for closure, will shift to Milton and Garner snack locations.
Its Memphis plant will discontinue production of plastic containers used for vegetable oil products, and use a third-party supplier.
Finally, the company’s taco shell production facility in Laval, Quebec, will close, marking ConAgra Foods’ exit from this business.
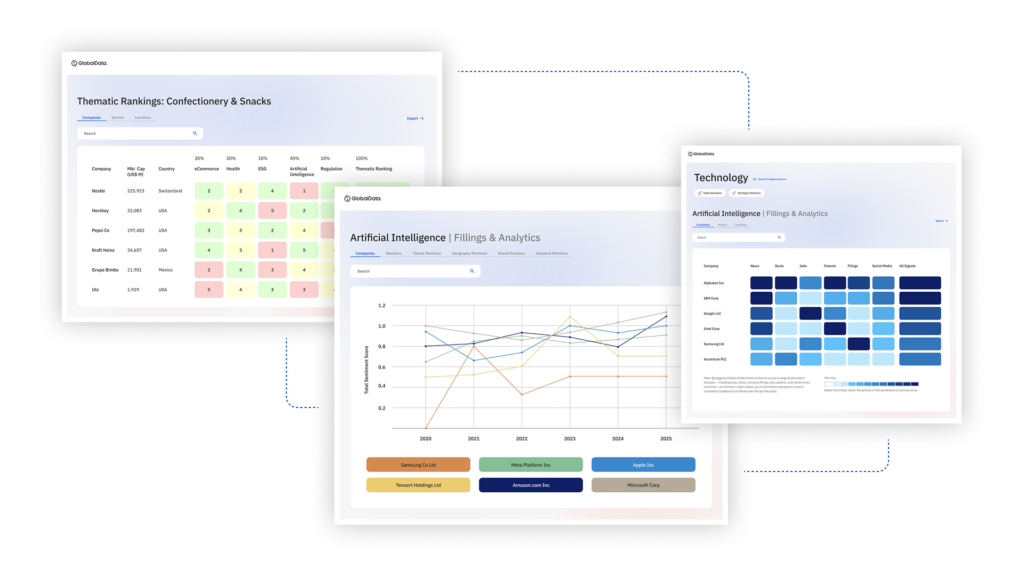
US Tariffs are shifting - will you react or anticipate?
Don’t let policy changes catch you off guard. Stay proactive with real-time data and expert analysis.
By GlobalDataConAgra Foods chief executive officer Gary Rodkin said: “Our rationalisation initiatives are designed to result in improved efficiencies and fixed cost savings that align with our strategy of strengthening long-term operating performance. This is another key element in achieving a more efficient cost structure that will fuel growth by allowing more focused investments in marketing and innovation.”
The company said it has made these actions to help streamline operations, reduce operating costs, improve capacity utilisation and improve gross margins, and plans to construct a new facility in Forth Worth to absorb some redistributed volume of canned bean, chili and pasta products from the six facilities.
Changes will be implemented over the next 12 to 18 months, with its total plant rationalisation expected to result in a US$100m reduction in annual fixed costs.