The Occupational Safety and Health Administration (OSHA) and Tyson Foods, Inc. (NYSE: TSN), joined together yesterday in a groundbreaking partnership to work cooperatively on worker safety and health programs at two Tyson facilities.
The five-year agreement, signed in Little Rock, Ark., establishes a joint OSHA/Tyson partnership team that will explore ways to enhance safety programs at Tyson processing facilities in Clarksville, Arkansas, and Monett, Missouri.
“The partnership formed today is an example of public-private cooperation that protects America’s workers,” said acting OSHA Administrator R. Davis Layne. “We believe the agreement will reduce injuries and illnesses at both of these facilities. And, we’re confident that the lessons learned from the partnership will translate into improved worker protections throughout the entire Tyson family.”
John B. Miles, OSHA Regional Administrator in Dallas said, “Management commitment and employee involvement will continue to be central elements to the implementation of an effective safety and health program.” Miles will be present for the signing.
Under the agreement, OSHA will work with senior staff, site management and employees to identify actions that will strengthen the Tyson Foods safety and health programs.
“We believe this effort will offer new ways and opportunities for us to work together and focus cooperatively on the thing that’s most important to all of the partners — the health and safety of our team members,” said Greg Lee, Tyson Foods chief operating officer.
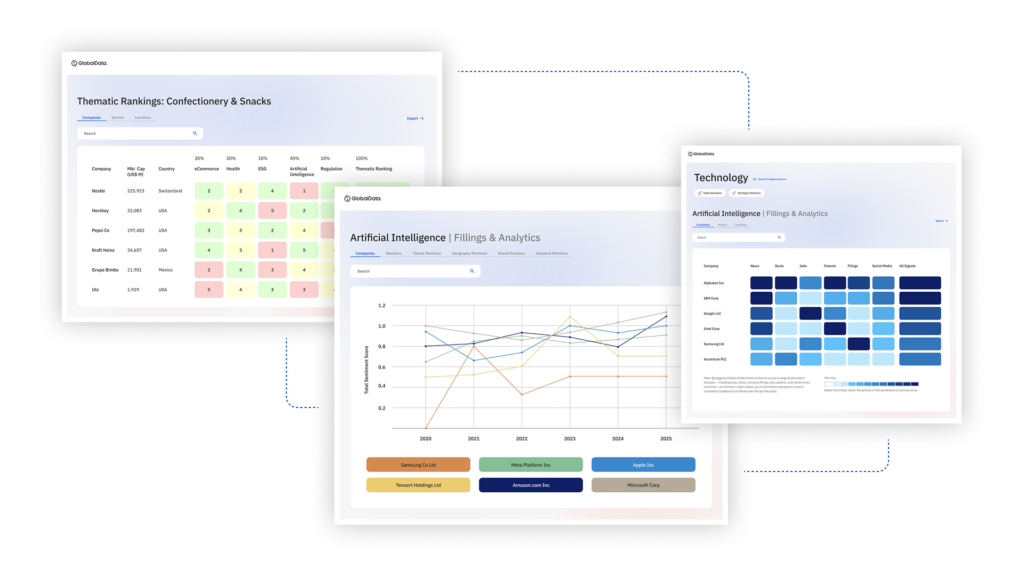
US Tariffs are shifting - will you react or anticipate?
Don’t let policy changes catch you off guard. Stay proactive with real-time data and expert analysis.
By GlobalDataTyson Foods, Inc., headquartered in Springdale, Arkansas, is the world’s largest fully integrated producer, processor and marketer of chicken and chicken-based convenience foods, with 68,000 team members and 7,000 contract growers in more than 100 communities. Tyson has operations in 18 states and 16 countries and exports to 79 countries worldwide. Tyson is the recognized market leader in almost every retail and foodservice market it serves. Through its Cobb-Vantress subsidiary, Tyson is also a leading chicken breeding stock supplier. In addition, Tyson is the nation’s second largest maker of corn and flour tortillas under the Mexican Original® brand, as well as a leading provider of live swine.
For more information, contact Tyson’s director of media and consumer relations, Ed Nicholson at (501) 290-4591, or email ed.nicholson@tyson.com.
Keeping Our Team Members Safe and Healthy
* Each year, Tyson Foods, Inc. invests (very conservatively figuring)
between 15 and 20 million dollars in safety and ergonomics programs.
* Every plant facility has a full time safety director and several
nurses, whose responsibilities not only include addressing work-
related injuries and illnesses, but also to monitor and improve
on-the-job wellness.
* Production workers go through an orientation and training program
which places heavy emphasis on workplace safety. Throughout Tyson,
the average time spent in this program is 1 1/2 days per production
team member.
* Each Tyson facility has at least one, and can have several safety-
related employee groups to address the specific safety requirements of
that facility. The groups include General Safety, Ergonomics,
Haz-Mat, and Fire Force Committees. They are underwritten by the
company and comprised of both hourly production workers and management
who know the workplace and can readily identify where improvements can
be made. Their efforts and input are fully supported by management.
* As evidence of the effectiveness of Tyson’s commitment to safety,
44 plants have topped the one million consecutive work hour mark with
no lost workday accidents within the past five years. Many of these
plants have reached the milestone repeatedly, several achieving two,
three, four and even five million consecutive safe manhours. Our
Dardanelle, Arkansas plant holds the Arkansas record of more than
seven million consecutive work hours without a lost workday accident.
Tyson’s workplace injury and illness lost workday record (according to
the U.S. Bureau of Labor Statistics) is safer than that of all
manufacturing industries combined.