
Food manufacturers continue to grapple with cost inflation and, as a result, are exploring new ways of manufacturing and distributing products more efficiently. One tool that has made a relatively modest impact on the food manufacturing sector but could be set to make a significant impact in the future is the internet of things (IoT).
A number of food groups have already implemented IoT sensors in their factories and supply chains and more are piloting the technology to see what other benefits it can bring.
Some tech experts believe that over the next decade IoT devices could become pervasive in manufacturing, which is borne out by some forecasts. GlobalData estimates the global market for IoT will hit US$1.1tn in revenue by 2024 – a significant increase on the $622bn recorded in 2022.
Food manufacturers’ use of IoT on rise
IoT is not a new concept. It’s been quietly used by manufacturers spanning multiple different industries for years but, in the last decade or so, the general public’s awareness and understanding of the technology has grown significantly thanks to more homes being fitted out with all manner of smart connected devices, from thermostats through to doorbells.
In layman’s terms, IoT refers to a series of smart devices connected to one another via the internet. In a manufacturing setting, IoT typically consists of a bunch of sensors fitted throughout factories that can monitor things like temperature, movement and noise.
Although the adoption of IoT by food manufacturers may have been slow compared with adoption rates in other sectors to date, according to Keith Thornhill, who heads Siemens Digital Industries’ work with the UK food and beverage industry, the implementation of the technology is now starting to pick up pace.
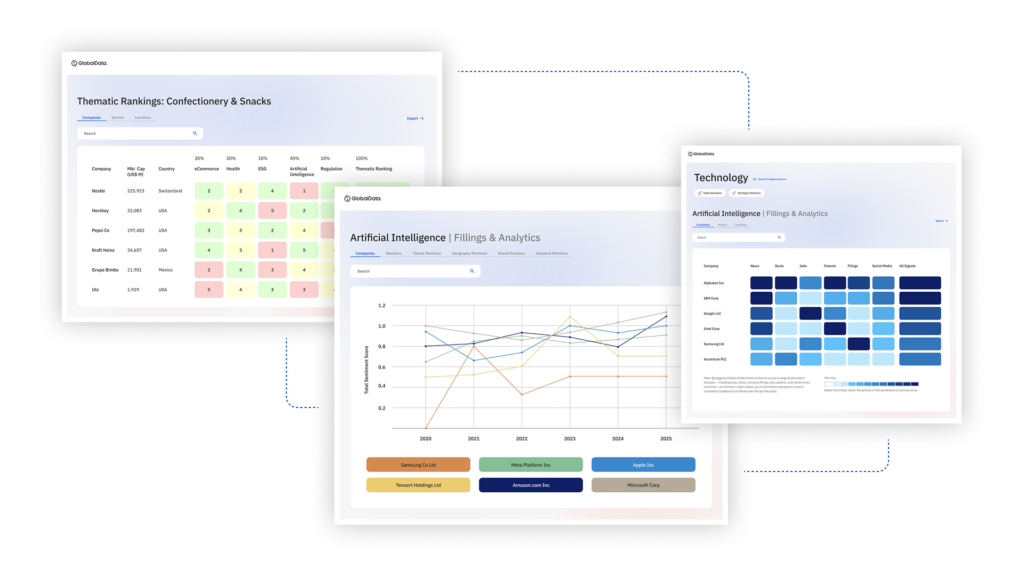
US Tariffs are shifting - will you react or anticipate?
Don’t let policy changes catch you off guard. Stay proactive with real-time data and expert analysis.
By GlobalData“It is clear that to measure is to manage, so a greater emphasis on real-time data connectivity across all parts of manufacturing is essential to better understanding operations,” says Thornhill. “But it’s not just manufacturing lines that produce data: buildings can produce huge amounts of data on usage, temperature and more.
“Factories, no matter their size, have become huge data centres with great potential for collecting valuable insights in all areas to optimise production. With this, manufacturers are gradually understanding the need to process this production data on an even larger scale.”
IoT technology isn’t just being rolled out in factory settings. Melody Dunn, director of global distribution industries at IBM Technology, which operates the Watson IoT platform, says there are lots of other use cases for the technology in the food industry.
“The internet of things is emerging as the saviour that promises to bring data from on-field sensors, aerial drones, and weather data together to generate actionable insights for the agri business, leading to improved yield quality, quantity, and resource utilisation,” she says. “We are also seeing this in food manufacturing, ensuring the quality and safety of consumer products. IoT is also being used to monitor refrigerators at retail stores and in trucks to ensure food safety throughout the distribution of food products.”
Touting benefits of IoT tech
The results enjoyed by some food groups that have already implemented IoT technology makes for impressive reading. Siemens is working with food and drink manufacturers on IoT projects. Thornhill says confectionery manufacturer Kinnerton increased productivity on one line by 15% after putting in place a “totally integrated automation solution” with data connectivity. He adds: “On a larger scale, a Nestlé factory in Juuka, Finland now saves up to EUR100,000 per year thanks to technology investments in data connectivity.”
Nestlé is one of the leading users of IoT in the food industry and, in the last two years alone, it has installed approximately 5,000 sensors to provide predictive maintenance capabilities in its factories.
“We have [also] deployed energy metering and monitoring sensors in more than 100 factories to drive energy efficiency,” says Howard Baker, head of engineering services and technologies at Nestlé. “We have used sensors to help us track and trace materials through our supply and manufacturing processes. And we routinely use [smart] sensors to monitor and optimise our critical process parameters ensuring quality and resource efficiency.
“As a result of these implementations, we have been able to reduce downtime, increase capacity, improve resource efficiency (GHG, energy and water) and improve the quality of our products for the consumer.”
Another of the major food manufacturers that has implemented IoT technology in multiple parts of its business is dairy giant Arla Foods. Thanks to its vertically integrated supply chain – from milk production at its farms through to the factories where the milk is processed and packaged – it has enjoyed numerous benefits from rolling out IoT.
“What IoT gives you is a precision and resolution of data that you were not able to capture before or you may have been doing manually,” says Tamas Toth, head of global supply chain IT at Arla. “For instance, you might load the milk at the farm and pump it in the tanker, and the driver of the tanker fills out the paperwork around how many litres of milk he has taken delivery of. However, he might write down a six on the paperwork, but he meant to write down an eight. IoT does not make mistakes so you can eliminate the usual 10% human manual error.”
Toth says one of the big use cases for Arla at the moment is metering energy and figuring out energy consumption and waste hotspots. “To make powdered milk, you have to dry the milk and evaporate a lot of water, which is very energy intensive,” he explains. “By using IoT and AI, we can control the process and regulate the temperature in a high frequency to ensure it’s the correct required minimum temperature rather than just turning the burner on maximum, medium or low. That can make a huge difference in terms of energy savings – double-digit percentages of savings.”
“Some way to go”
One of the big untapped opportunities for food manufacturers is the ability to have machines talk to one another at a speed that wasn’t possible before and this connectivity allows vital decisions to be made within seconds.
“Manufacturing sites can now leverage information that they couldn’t see before, near real-time, and it can empower them to make better decisions about line performance and product quality, improving service to customers and ensuring consumers have a great product experience,” says Bob Schug, vice president of digital services and supply chain at Mondelez International, which is using IoT in different areas of the business.
According to Schug, a benefit of IoT technology for food manufacturers is the sensors are affordable, flexible and portable and they can cost-effectively solve some big problems, particularly for more traditional manufacturers that so far have been slow to embrace technology.
“I think it can feel quite daunting for companies that have grown up in an analogue age and are looking at a full digital transformation,” says Schug. “This [IoT] unlocks options that we didn’t have even a few years ago, to transform without a giant capital re-platforming of some legacy equipment that is still very useful and working really nicely.
“It helps us understand where could we add a digital signature or put a digital component in our making operation or logistics operation where we can really learn and get more effective – and it’s affordable enough and approachable enough that this will be pervasive over time.”
At the moment, technology experts say food manufacturers have barely scratched the surface in terms of fully exploiting the potential benefits IoT technology offers. “Recent research by Siemens found that 81% of food and beverage manufacturers in the UK and Ireland are exploring more ways of capturing, managing and analysing production line data, but despite high uptake and good intentions, just 38% of manufacturers agreed that they had ‘somewhat’ achieved data maturity,” says Siemens’ Thornhill. “We still have some way to go.”
Schug agrees. He believes that, in the future, IoT will become omnipresent in manufacturing and distribution environments. “I think there are many, many use cases that help us start connecting end-to-end some processes that before were fairly siloed,” he says.
“If you look at a traditional supply chain, often what happened in the warehouse stayed in the warehouse and what happened in the manufacturing plant stayed in the manufacturing plant. And, what these amazing advances in technology do, is they now let us connect things, almost in real-time, in a way that we couldn’t do before and we can see some of the inefficiencies that we lost by optimising these different settings.”
It would appear there are opportunities still for food manufacturers to grasp and, with costs continuing to concern boardrooms, investment in IoT might be part of more companies’ efforts to mitigate that pressure.
The four stages of IoT development: How we get to a fully automated world