
There’s panic at the petrol pumps. A shortage of food on supermarket shelves. Energy prices are rapidly increasing and smaller energy companies are going bust as a result. And fresh fruit and veg is rotting in farmers’ fields across the land. Welcome to Brexit Britain where issues that existed prior to the UK leaving the EU have been exacerbated by the country’s departure from the bloc and the ongoing Covid-19 pandemic.
A key reason for many of these issues is straightforward. There is a lack of workers to tend to the fields and pick and pack produce in factories and there’s a severe shortage of lorry drivers to drive HGVs delivering fuel to the pumps and food to our supermarkets. Many of these workers left the UK when it left the EU or during the pandemic – according to research from Grant Thornton around 1.3 million foreign-born workers have left the UK since the pandemic began. And because these jobs don’t tend to have attractive pay and incentive packages UK workers are simply not interested in picking up the slack. As a result, it’s placed the country’s grocery supply chain under intense pressure.
So what can be done to address these issues and ensure in the longer term they don’t continue to cause problems?
The supply chain challenges the UK grocery sector currently faces is the “cumulative impact of a series of major challenges”, Shane Brennan, chief executive of the Cold Chain Federation, says. He points to the “disruption from post-Brexit customs changes, changing customer needs as sectors are recovering from lockdown in different ways and at different paces, the workforce shortage – which extends beyond driving and into warehouses and back offices, too – and now also the fallout from the energy and CO2 crises”.
For some sectors, the challenges Brennan outlines are not a new thing. The shortage of qualified truck drivers in the UK – it’s estimated we need around 100,000 additional drivers – has been a problem for the industry for years and, as well drivers from EU states returning home, it was exacerbated by the pandemic as new drivers were unable to take tests during lockdown.
A spokesperson for The British Meat Processors Association (BMPA) says the problem of labour shortages in the meat industry is also a long-standing issue.
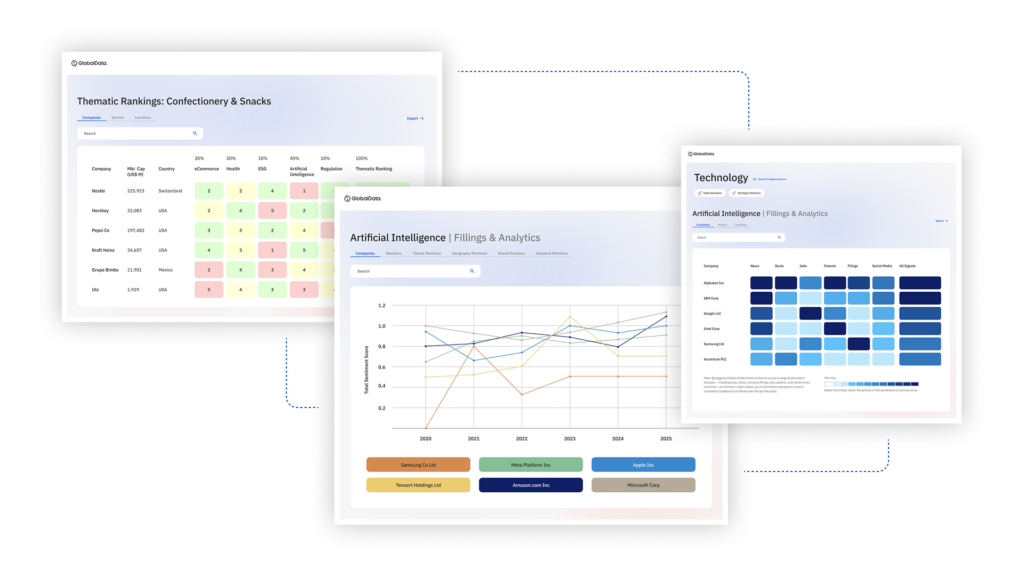
US Tariffs are shifting - will you react or anticipate?
Don’t let policy changes catch you off guard. Stay proactive with real-time data and expert analysis.
By GlobalData“Meat processing, by its very nature, is labour-intensive and difficult to automate because of the flexibility, dexterity and judgement of a skilled butcher that’s needed on parts of the production line,” explains the spokesperson. “It can also be physically challenging. which reduces the number of suitable candidates. For a long time, British people have been generally reluctant to enter the industry and available workers are often not situated in the right geographical location and are reluctant to re-locate.”
The fallout from these issues is manifesting itself in different ways for manufacturers. Most approached to comment on the problems declined, but the response from John Want, UK sales, marketing and R&D director at US-headquartered Rich Products, is typical of the situation many food companies find themselves in.
“The shortage of drivers and delays at ports is affecting our inbound ingredients, packaging and delivery schedules,” says Want. “So, although we are not short of anything, we are having late deliveries, or part deliveries, and late notification of those deliveries. From our perspective, the most problematic issue is planning production and being flexible in production. We are at the stage of making what we have the ingredients for, rather than what we should be making to fulfil customer orders. And then there are the problems with our customers getting product to stores from their warehouses, which has a knock-on effect on our sales out to them.”
Moving beyond short-term fixes
So what can be done to tackle these problems?
Brennan says there are some short-term solutions that could help relieve this pressure such as the UK government implementing a visa scheme that would make it simpler and quicker for EU citizens to return to the UK to fulfil crucial roles where there are shortages. Earlier this week, the Government announced plans to allow up to 5,000 truck drivers and 5,500 poultry workers to enter the UK on short-term visas in a bid to help alleviate some of the pressures affecting industries.
“However, many of the challenges the grocery supply chain faces are due to permanent change,” adds Brennan. “The labour shortage is chronic with no quick fix, and we won’t even start seeing Brexit impact the goods we buy until 2022. People’s lives have changed and the food supply chain needs to adapt to consumers’ changing needs. We also need to accelerate towards energy efficiency and net zero. Returning to ‘normal service resumed’ is just not the cold chain’s reality. The only option is to find a new path forward for the long-term.”
Brennan adds transitioning away from our reliance on labour from overseas needs to be at the heart of this new path. He argues there needs to be realism “about what the Government can and will do, as an industry we need to make changes happen ourselves”, adding: “Wage price increases, recruitment and training programmes, investment in automation and fundamental reorganisations of resource and supply chains will all become prominent features of our industry from now on.”
This is likely to have an impact on consumers as retailers start to increase prices, simplify ranges and prioritise the goods they stock based on what is available.
“Ever cheaper food, available however and whenever consumers want, will be neither the ambition nor the reality,” says Brennan. “Government, the grocery supply chain and consumers must work together to evolve the old model into a more sustainable approach that works for consumers, for businesses and the people who work in them, and for the UK’s net-zero goals.”
Changes ahead for UK labour pool
Speaking specifically about the challenges facing the meat-processing industry, the BMPA spokesperson says there is a “degree of unfamiliarity and misunderstanding that surrounds the meat industry, so there’s a job to do to re-introduce the sector to British workers and demonstrate the breadth of secure, full-time career opportunities available”. However, they say those efforts will take time – it takes 18 months to train a new recruit to become a fully qualified butcher.
“This work has already started, but it’s far from clear – especially given the current labour crisis both here and abroad – that it will bear fruit quickly enough,” says the spokesperson. “If that’s the case and no short-term support is forthcoming from government in the form of access to migrant labour, we will see this key industry diminished and Britain’s food security weakened.”
Andy Searle, a managing director and partner at management consultants AlixPartners, says one of the key things that needs to be quickly established is where do we, as a society, see value in the supply chain and who should attract that value. He cites the example of truck drivers.
“You have to make the case for people choosing a job as an HGV driver and that value is not just monetary, but it’s also the perception of some of these jobs so that people see it as a career. So there needs to be a shift,” says Searle.
It’s a view shared by Clive Black, director at Shore Capital and an equity analyst covering the UK food and grocer sector. He says: “Frankly, we have paid too little for someone who was driving a 40-tonne truck on our roads, which is quite a dangerous item in its own right, and we’re going to have to pay more for that. Going forward, some of the impulsive requirement for next-day delivery and delivery tonight, is going to maybe not come into question, but it’s going to cost more. And therefore we’re going to have to start paying more for labour, we’re going to have to probably start paying more for services. In that respect, I think there will be a reasonably long shadow of this combination of Brexit and Covid.”
The question is who will ultimately bear the financial strain of these costs increases. “Who is really going to pay for that in the end and whose margin does that come out of,” says Searle. “My worry is that this all settles down in a few years and the fundamental issues never really get addressed and so we’re then no more resilient when another shock comes along.”
Black envisages major changes occurring to the UK’s labour pool over the next few years as companies look to address some of the challenges they currently face. He thinks going forward there will be fewer temporary agency workers and more permanent employees and people who are trained in-house.
“Clean pieces of paper that can be part of a business’s future,” says Black. “For example, a number of businesses have started to create their own driving academies purely to take control.”
He thinks these permanent workers will be better paid but there will be fewer of them as more companies introduce greater levels of automation into supply chains.
“For a long time, economists who couldn’t run a bath, never mind run a business, have been telling the British that they’re very unproductive. That’s fine when you measure productivity only in terms of labour but, when labour is effective, production is cheap, and it made sense for businesses not to over-capitalise their businesses or their organisations through automation,” Black asserts.
“However, labour is being repriced and structurally repriced and it has been going this way for some time, with the national living wage going up well ahead of inflation for some time. The present labour shortages sort of build upon that. So, automation is going to come in much more aggressively and in a much more wider context than I think we would have thought of a year ago, and businesses that were maybe ambivalent or had it quite far down their to-do lists have raised it up the to-do list. So, I think were absolutely going to see an acceleration of automation over the next two or three years.”
However, in the short term, manufacturers, trade bodies and industry analysts alike all agree the UK food industry is likely to experience continued pain in the supply chain before these issues can be addressed.
“Christmas 2021 won’t be cancelled, but it’s going to be a different Christmas and it was totally avoidable,” says Black. “This is not about Brexit. This is about a government actually saying how many lorry drivers do we need and do we have the wherewithal to employ them in the UK? How many pickers do we need and do we have the wherewithal to pick products in the UK? It’s about being honest about the fact a lot of British nationals will not do that work and stating why, and then having a conversation with the public and the industry.
“It is abject failure. What’s happened here was avoidable but there is no quick fix and, because the boil hasn’t been lanced, it is going to be a much more painful and messy situation.”